PRECISION HIGH-QUALITY
ALUMINUM ANODIZING
What Is Anodizing Type 2?
Aluminum anodizing is a controlled electrochemical process that increases the thickness of the oxide layers that naturally exist on aluminum surfaces, improving corrosion resistance.
We offer Type 2 and Hardcoat Aluminum Anodizing Type 3.
Class 1 and 2; MIL-A-8625 and MIL-PRF-8625.
We meet tight tolerances using precision control systems to achieve accurate coating thickness of aluminum anodized parts.
The most common aluminum anodizing creates a coating thickness of up to 1mil. We seal dyed components, which increases corrosion resistance and reduces fading.
Type 2 Coating Thickness: .0001 to .0015 mil
Type 3 Coating Thickness: .002 to .0015 mil
Regular Nadcap reviews and audits ensure compliance with AC7004 requirements for the aircraft, space, and defense industries.
Current Lead time Avg: 3-5 days
Clear
Orange
Grey
Black
Red
Gold
S.D. Green
Tan
O.D. Green
Green
Blue
Purple
Copper
Pink
Benefits of Type 2
-
Aluminum anodizing Type II creates a protective oxide layer that bonds directly to the aluminum surface, making it highly resistant to environmental elements like moisture and salt. This layer significantly reduces the likelihood of corrosion and extends the lifespan of the metal, making it ideal for use in outdoor or harsh environments. The anodized surface is non-reactive, further protecting the aluminum from deterioration.
-
The anodized layer not only preserves but enhances the visual appeal of the aluminum. Anodizing Type II allows for easy dyeing, offering a wide range of colors and finishes that are more durable than those achieved through painting or powder coating. The process provides a smooth, uniform look that resists fading and chipping, ensuring the aesthetic quality is maintained over time.
-
Anodizing results in a hardened surface layer that is significantly tougher than untreated aluminum. This increased hardness enhances resistance to scratches, wear, and abrasion. This durability makes anodized aluminum ideal for high-traffic applications, from architectural panels and consumer electronics to industrial machinery components.
-
The anodized layer acts as an excellent electrical insulator due to its non-conductive properties. This is particularly valuable in electronic applications where isolation between conductive components is required. The natural oxide film ensures that the anodized aluminum can be used safely in environments where electrical conductivity would be detrimental or hazardous.
-
Anodizing can serve as an effective masking layer that resists the adhesion of certain materials and treatments. This property can be particularly beneficial during processes that require selective application, such as painting or adhesive bonding. The anodized layer’s resistance to chemicals and environmental exposure enhances its utility as a protective mask for other operations.
-
The anodizing process is relatively environmentally friendly, as it does not involve heavy metals or produce hazardous by-products. Additionally, anodized aluminum is recyclable and contributes to sustainable manufacturing practices.
-
Anodizing provides a porous surface that helps coatings, sealants, and adhesives bond more effectively. This property makes anodized aluminum a superior substrate for painting or powder coating, improving the overall finish and long-term adhesion.
-
The anodized layer improves the heat dissipation properties of aluminum, making it useful in applications where temperature control is essential, such as heat sinks and other thermal management components.
-
Anodized aluminum requires minimal upkeep due to its durability and resistance to staining or fingerprints. The material can often be cleaned with just water and mild detergent, making it cost-effective and easy to maintain.
-
The anodized coating offers resistance to ultraviolet (UV) radiation, which helps prevent discoloration and degradation over time. This makes it an excellent choice for outdoor applications where prolonged sun exposure is expected.
Dark O.D. Green
Black
Grey
O.d. Green
Dark Grey
Dark Tan
Tan
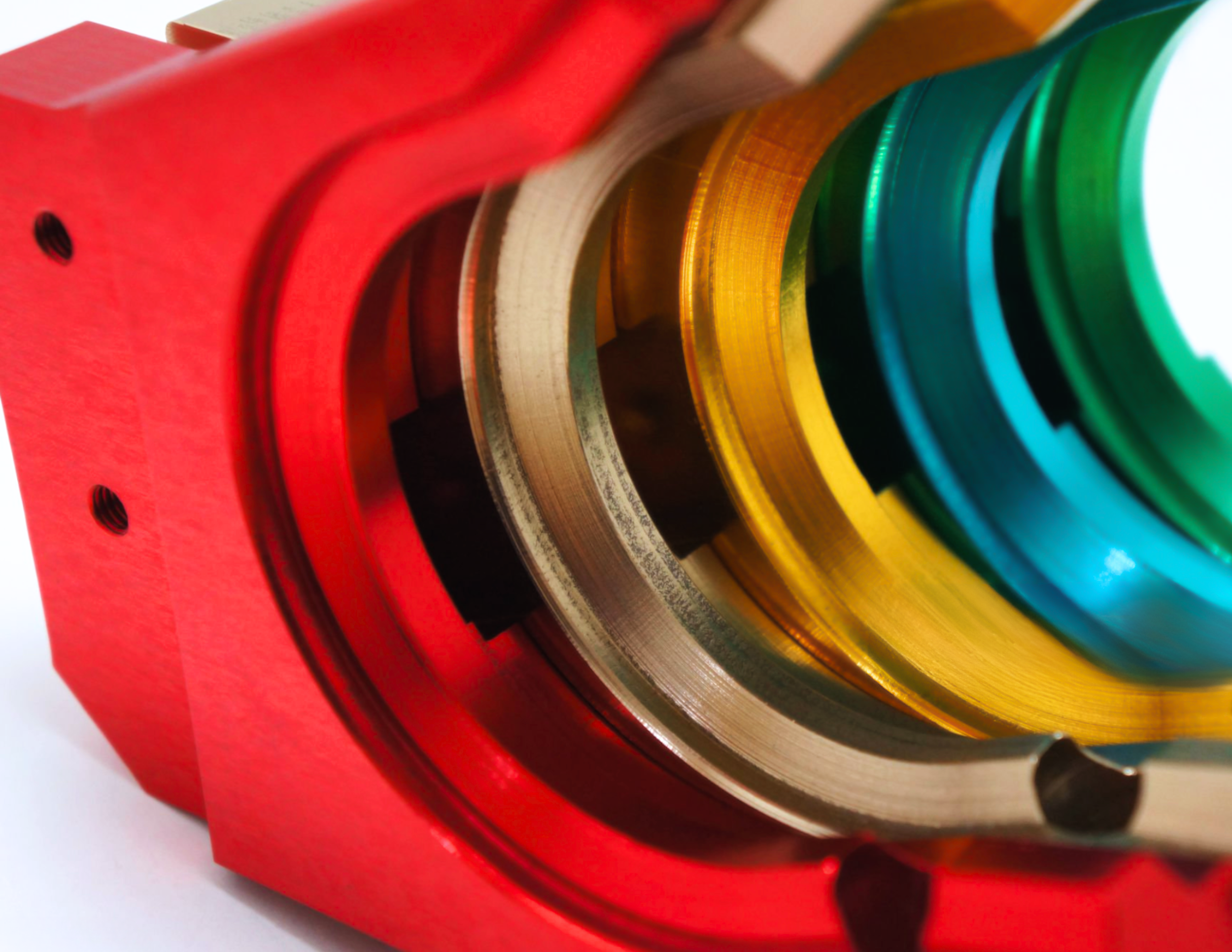

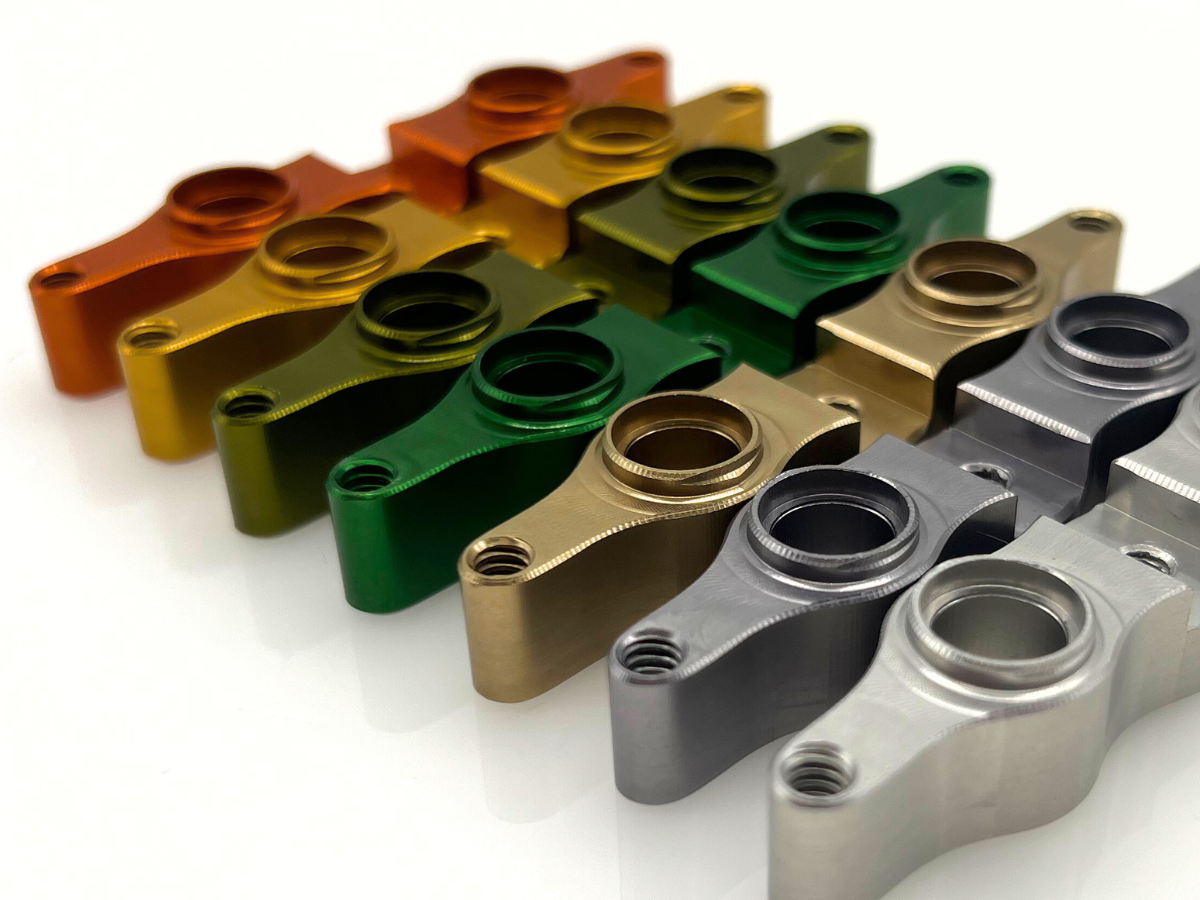
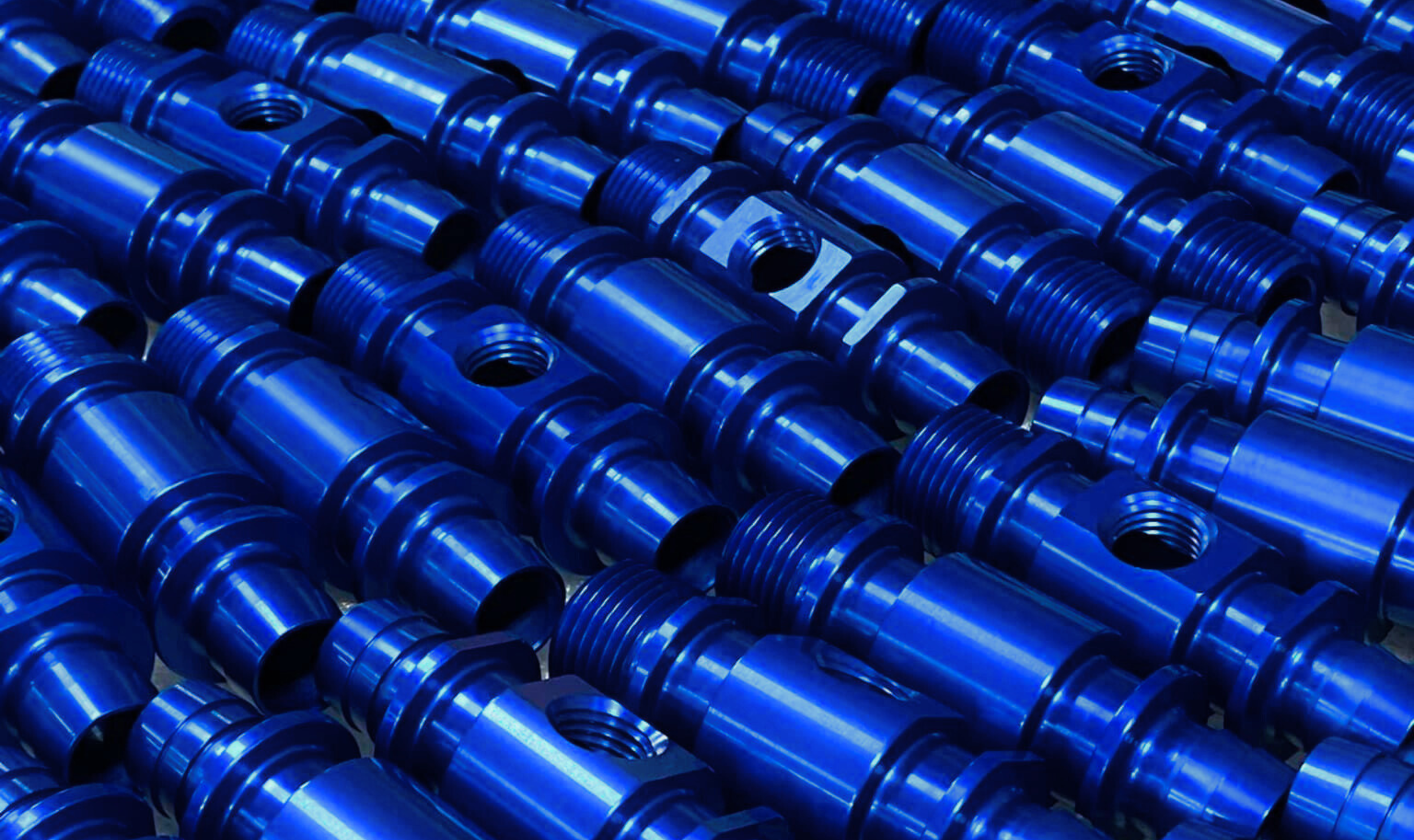


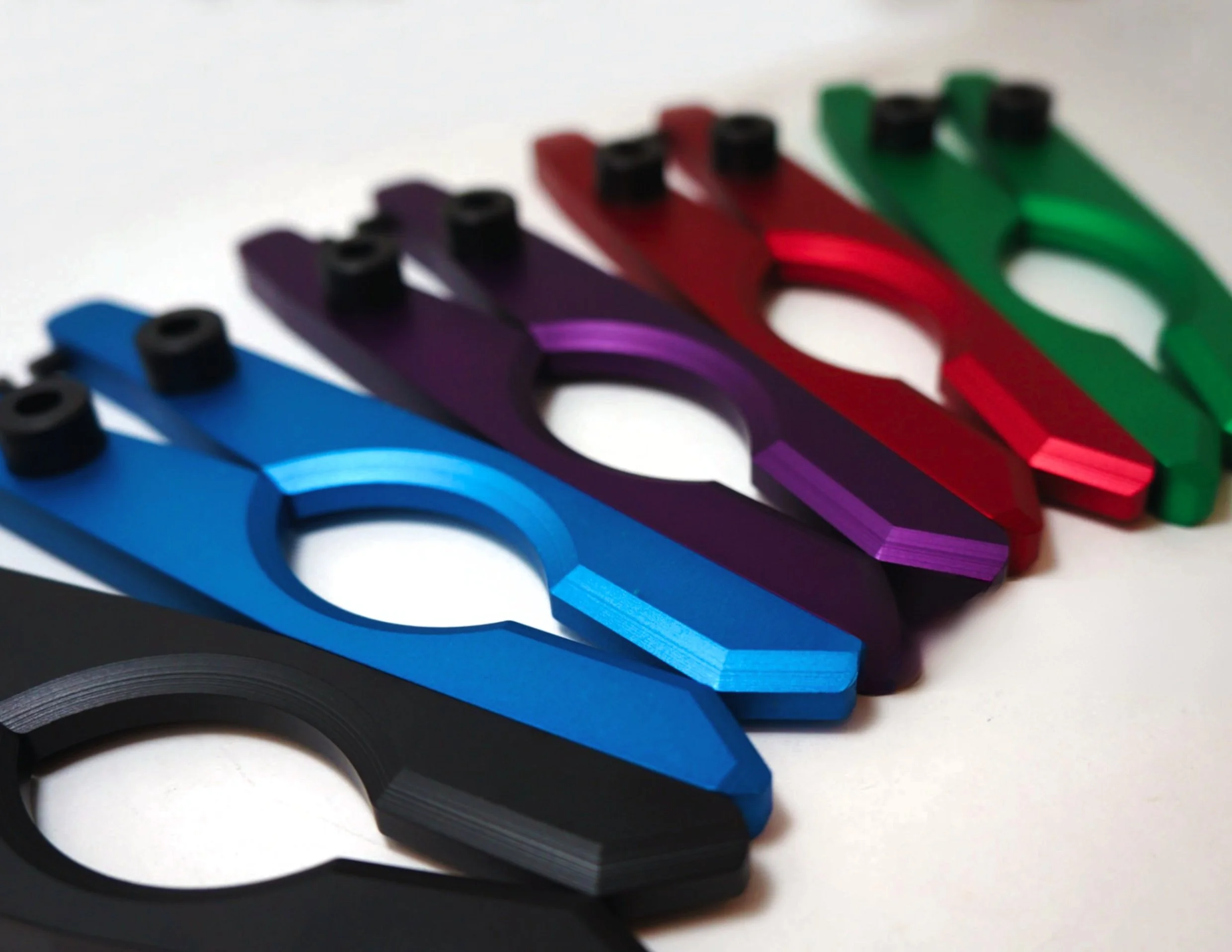





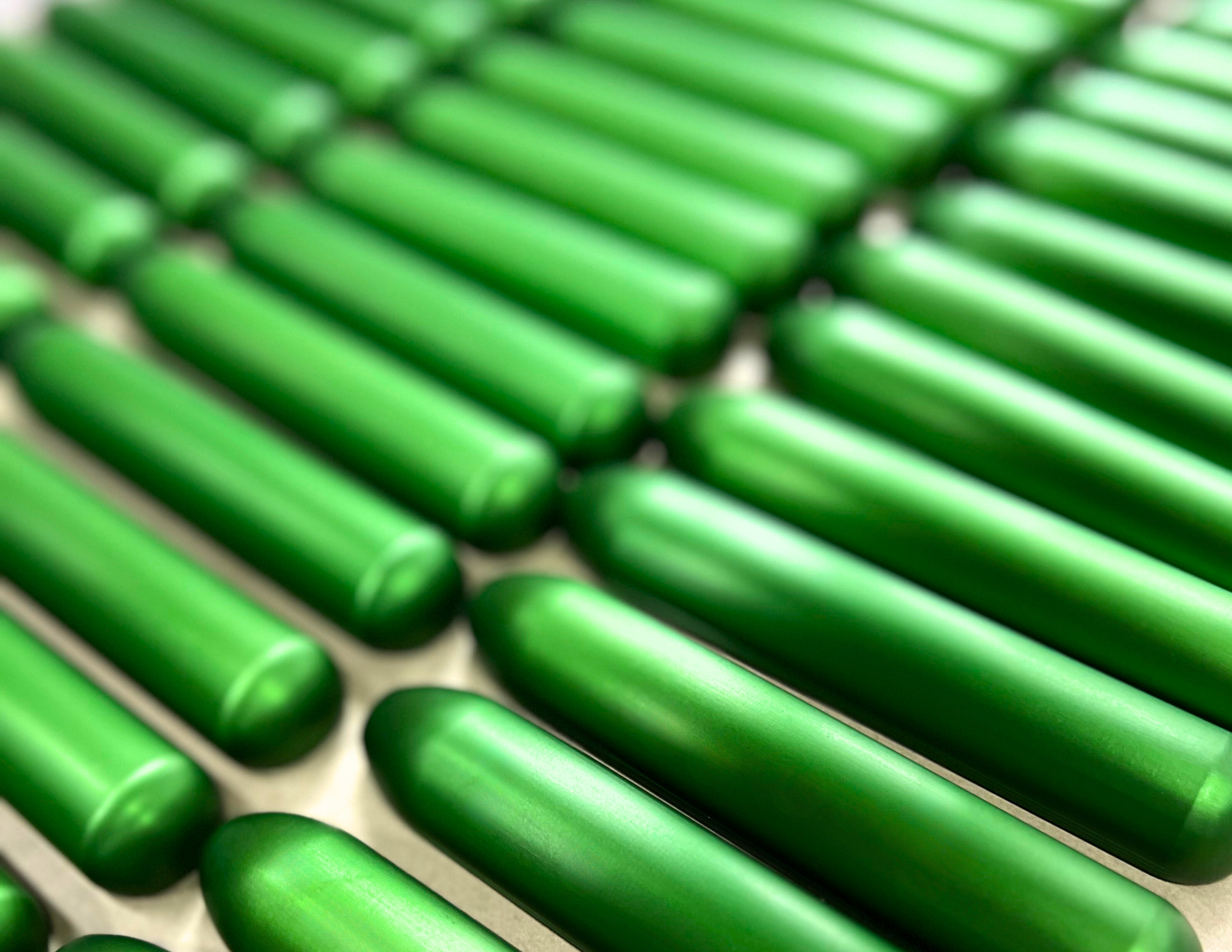








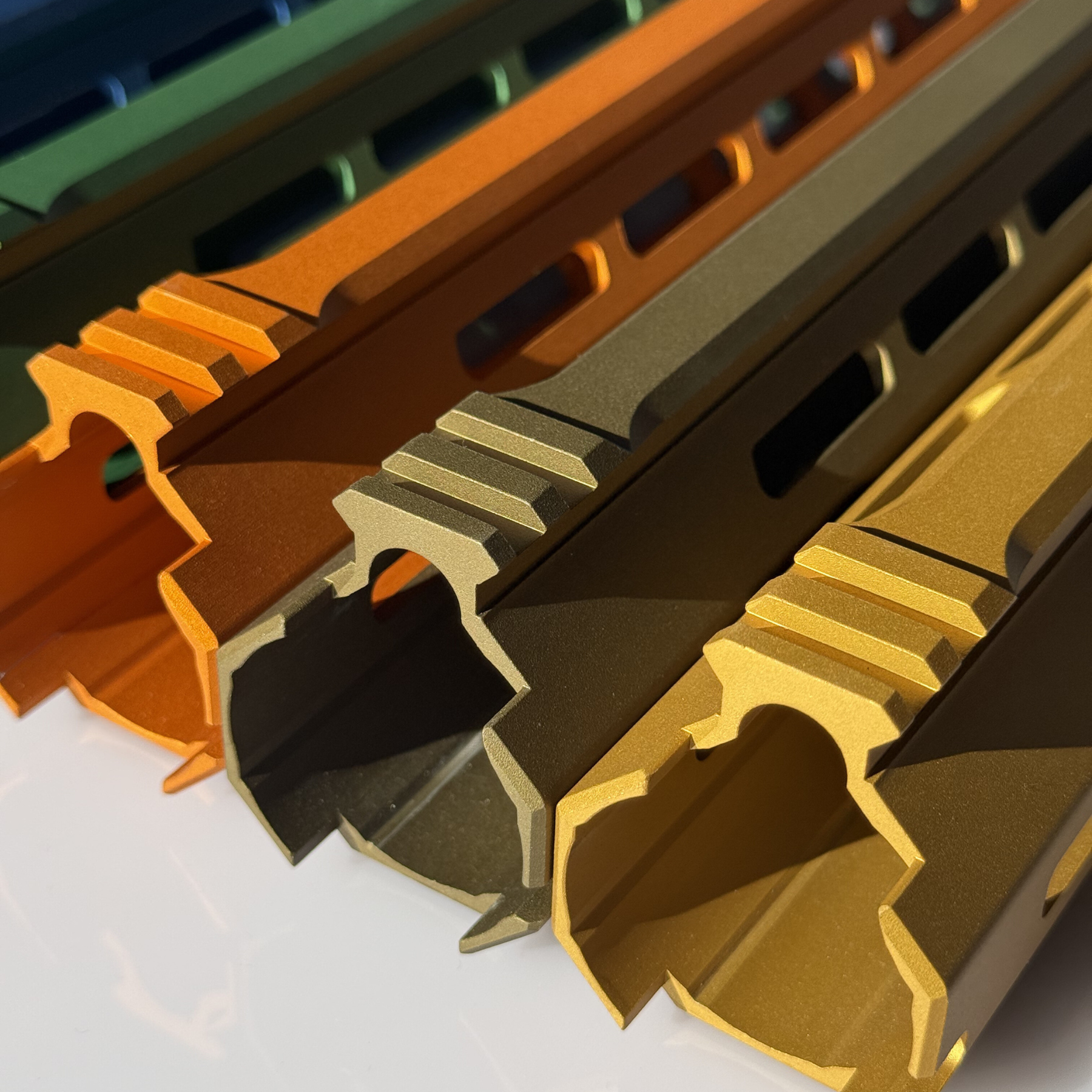
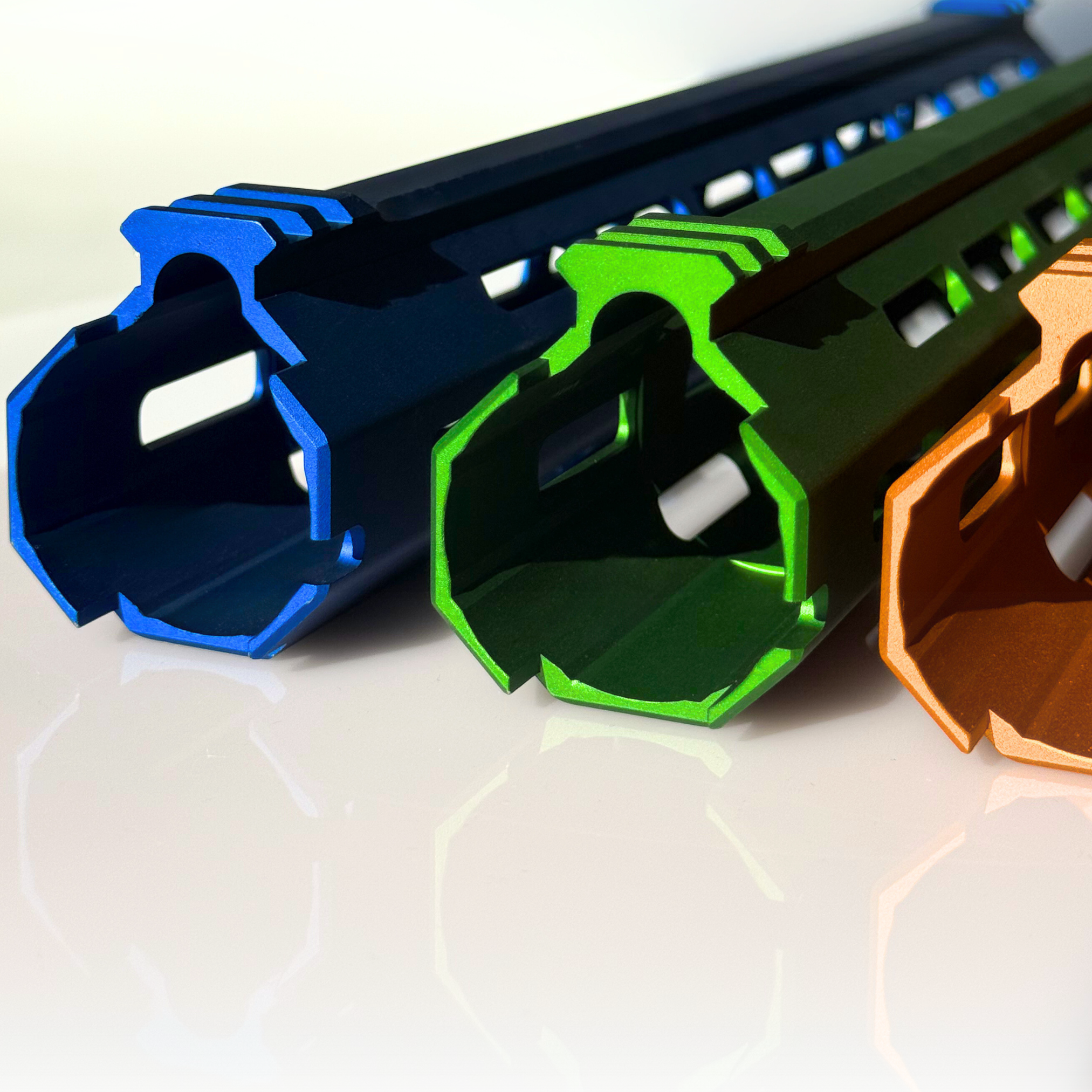
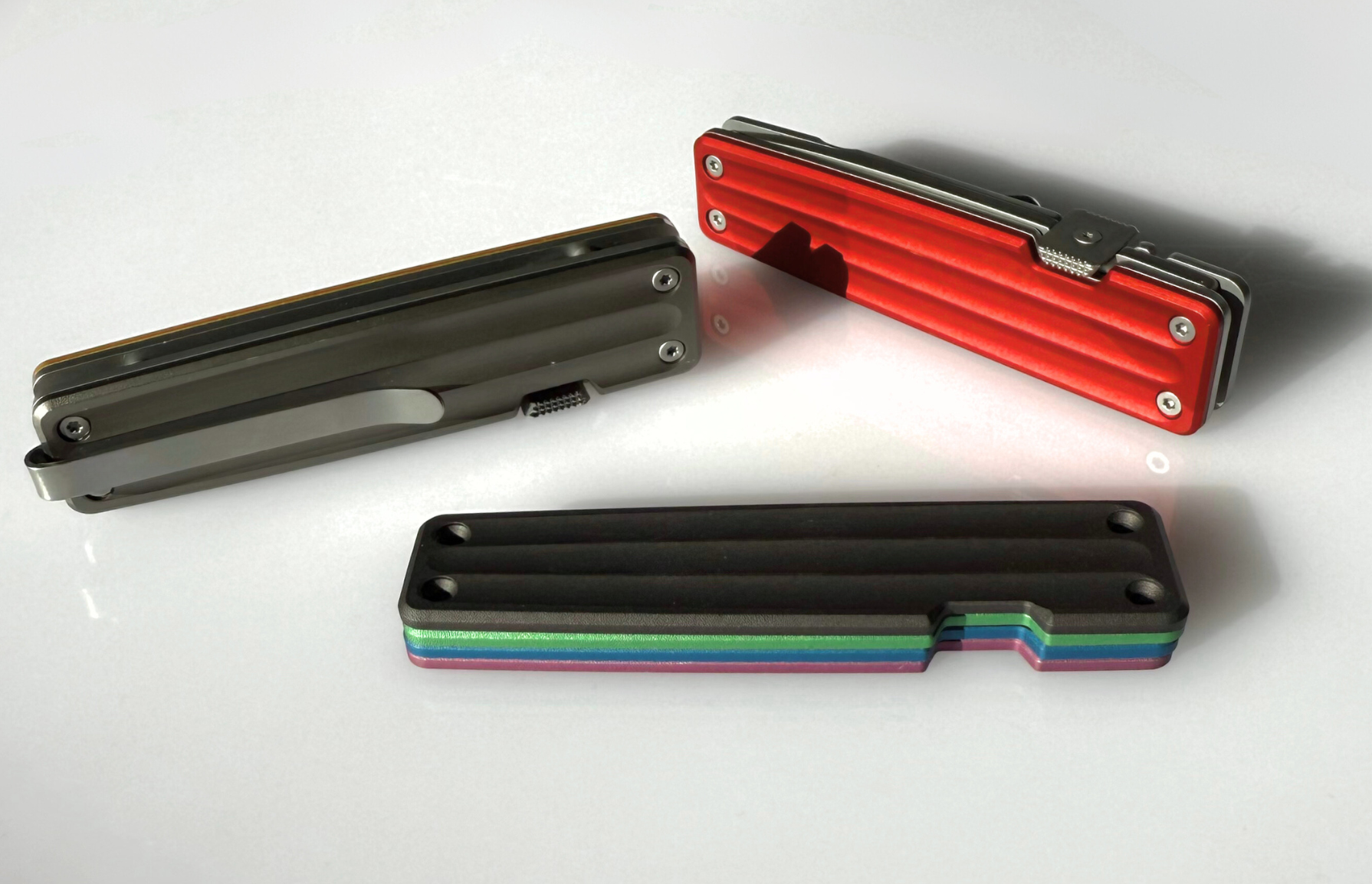
FAQs
-
Yes. There are a few options when it comes to Anodize Masking such as Laser Marking, tapes, custom caps, and masking moldings.
See Masking Method(s) Blog Post Here
-
Type II
Standard anodized aluminum has a coating up to 1 mil thick and is sealed to seal in the dye and close the pores after the anodizing process for improved corrosion resistance. It is the most common form of aluminum anodizing and is available in dyed and non-dyed options.
Type III
Hard Coat Anodized Aluminum is a thicker, more durable coating up to 2 mils thick. It is also available in non-dyed and dyed options. For the best wear resistance and when adhesion is required on a non-dyed component, it is typically not sealed.
-
When anodizing aluminum parts with tight dimensions, it is important to understand that the coating will affect the final dimensions. In general, 50% of an anodized coating will penetrate the material’s surface, and 50% of the coating builds up on the surface. But, the change in final dimensions is determined by the thickness of the coating.
-
Class I coatings have a mil thickness of 0.7 (18 microns) or greater for aluminum anodizing. Class II coatings have a minimum mil thickness of 0.4 (10 microns). Class I coating is a high-performance anodic finish used primarily for exterior building products and other products that must withstand continuous outdoor exposure.
-
Nickle Acetate
Nickle fluoride
Hot Water
-
AC7000 – AUDIT CRITERIA FOR NADCAP ACCREDITATION
AC7108 REV I – NADCAP Audit Criteria for Chemical Processing
AC7108 Anodize; Hard Anodize and Sulfuric Anodize (Not for Metal Bond) – AC7108/8 must also be selected
AC7108 Chromate (non-hexavalent)
AC7108 Passivation
AC7108 Electropolish
AC7108 Standalone Cleaning
AC7108 Descaling
AC7108 Solution Analysis & Testing – AC7108/4 must also be selected
General Cleaning & Pre-Cleaning
Alkaline Cleaning
Chemical Cleaning
Titanium Cleaning
Emulsion Cleaning
Semi-Aqueous Cleaning
Solvent Cleaning
Ovens for Thermal Treatments – Heat Processing; Part Dying
Stripping of Coatings
Inorganic Coatings
Other Stripping
AC7108/4 REV C – NADCAP Audit Criteria for Solution Analysis and Testing in Support of Chemical Processing to AC7108
Solution Analysis (In Support of AC7108)
Testing Performed Internally (In Support of the Chemical Process Accreditation)
B05 – Salt Spray Testing (In Support of Chemical Process Accreditation)
B06 – Water Immersion / Humidity Testing (In Support of AC7108)
B09 – Taber Wear Testing (In Support of AC7108)
B10 – Adhesion Testing (In Support of AC7108)
B13 – Coating Weight Testing(In Support of AC7108)
B 14 – Conductivity Testing (In Support of AC7108)
B15 – Resistivity Testing (In Support of AC7108)
B16 – Coating Thickness Measurement (In Support of AC7108)
B23 – Other Testing (In Support of AC7108)
AC7108/8 – NADCAP Audit Criteria for Anodizing (Not for Metal Bond)
Anodized Aluminum, Hard Anodize
Anodize Aluminum, Sulfuric Acid
Dye
Seal
AC7108/11 – NADCAP Audit Criteria for Conversion Coating
Aluminum, Non-Hexavalent Chrome Alternatives
AC7108/12 REV A – NADCAP Audit Criteria for Standalone Cleaning, Descaling, Passivation, and Electropolishing
Passivation